Process Steam Efficiency the second Blog
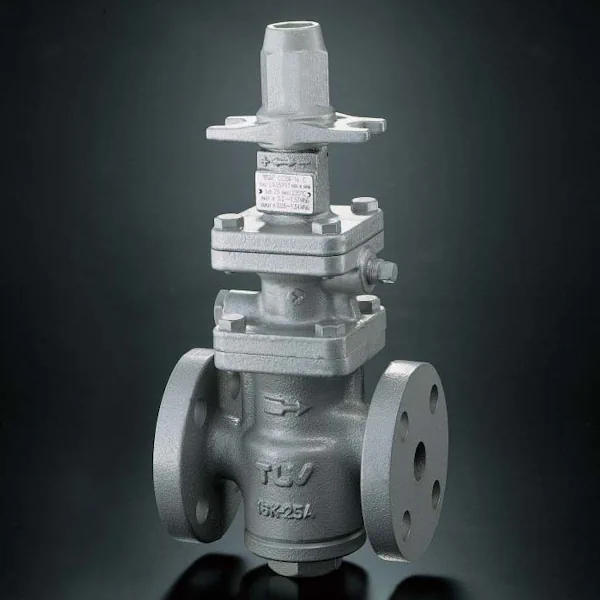
This will be the second in our mini-series of process steam efficiency blogs where we will continue to discuss how to improve your steam system and process steam efficiency. One of the biggest issues I come across personally working with many customers on process steam is that over the years many businesses have added more and more lines to already labouring steam systems without any thought to steam system capacity. In some cases I have come across in the past, systems that are already labouring are added to despite the best advice you can give about prioritising steam loads. In many cases businesses run with Steam Boilers well below the capacity required and on systems like this priming is a regular occurrence, especially when companies get busier than the norm. Avoiding these issues is easier to solve than you’d think, so for this and more information on process steam efficiency please take the time to click the read more icon or contact us for help and advice.
Process Steam Efficiency Surplussing Valves
Process steam efficiency is not always about reducing your energy bills or ensuring heat transfer is at maximum efficiency, sometimes it is just about prioritising certain processes on your steam system. If your business is like others outside of the steam user’s community sometimes or even more frequently your boiler capacity does not match your needs. The easy answer is to buy a new Steam Boiler or install an accumulator. Still, these are not always the most practical or within the budget of many businesses struggling to compete in a local, national or even international economy. Sometimes the most cost-effective answer is a steam Surplussing Valve, such a valve sized correctly and fitted to the appropriate steam line can prioritise certain processes or lines within your process steam system. The TLV SP-COS-R-16 Steam Surplussing Valve is a self-acting pressure control valve for use up to a maximum pressure of 16 bar and the unique design of the piston ensures high accuracy of control. All major components are made from stainless steel including the inbuilt strainer to protect the pilot valve. The internal pressure sensing channel makes external sensing unnecessary and results in a compact installation. This high-quality control valve is available by contacting us at Besseges (Valves, Tubes & Fittings) Ltd and we will ensure that your business receives the correctly sized valve promptly. For more information please click the highlighted link to download a data sheet on this product or contact our sales team to discuss your requirements.
Process Steam Efficiency Steam Trap Selection
One of the biggest issues to process steam efficiency can be poor steam trap selection which is far more common than most businesses realise. A very common example of this issue involves Thermolier Heaters, these simple steam coils in a metal box complete with a fan and shutters to distribute heat are fitted with a steam trap. The steam trap that should be installed on this and the majority of steam coils is a free float steam trap or float type steam trap, but so many sites just install the least expensive or a steam trap that happened to be on the shelf. More often than not these steam traps are cycling traps such as thermodynamic or Bucket type steam traps and are not the right choice for the application in our opinion. The constant flow of a free float steam trap on start-up will clear the coil of condense ensuring that the Thermolier is up to temperature quickly and efficiently. If such an error is repeated in a manufacturing process, the result can be condense logging, resulting in poor heat transfer and damage to process steam equipment. The result of these events is nearly always poor manufacturing outcomes and increased maintenance costs. Other avoidable events due to correct steam trap selection are instances of steam and air locking which will be covered in a later instalment of Process Steam Efficiency but one of the most common steam trap faux pas is incorrect orifice size. Steam trap orifice sizing is decided by the differential pressure, the difference between the pressure at the steam trap outlet and the back pressure in the condense return line. Back pressure in a condense return line can have several causes, if a steam trap is discharging to the atmosphere then the back pressure would be zero. There are many reasons for back pressure occurring on a condense line such as a rise from the process, for each metre of height there would be a 0.1 bar back pressure or even elbows fitted in the line would cause back pressure. If you take a simple example though of a 3-metre rise acting against a steam trap discharging at 5.0 bar, the differential pressure would be 4.7 bar as the back pressure would be 0.3 bar. When sizing TLV free float steam traps discharge tables are provided for different differential pressures ensuring that your business always receives the correctly sized steam trap to suit your process. For more information on this or any aspect of process steam efficiency please contact our technical sales team today.
The picture above shows the TLV line drain free-float steam trap, a product unique to TLV in the UK and one we recommend highly to our customer base. This highly efficient line drain steam trap offers rapid air release through efficient thermostatic air venting and works particularly well on systems with shallow dirt pockets. Other advantages over traditional thermodynamic steam traps are it is not prone to air locking and on start-up rapid clearance of condense is assured and very efficient. For steam trap sizing and specification for all process requirements please contact us and we will ensure your business receives the best advice available from the North of England’s leading TLV and steam ancillaries distributor, Besseges (Valves, Tubes & Fittings) Ltd.
For full details on what we can offer on double block and bleed solutions please read the double block & bleed blog by clicking the highlighted link or contact our sales team to discuss your requirements. The double block and bleed system in the above photograph is in service at one of the UK’s leading corrugated packaging plants and in addition to providing the double block and bleed valves, we ensured safe testing of the system by supplying quick-release steam hose and a flanged sight glass with flow indicator.
Register For An Account
Save & manage your details, access invoices, and enjoy a quicker shopping experience!