Improving Process Steam Systems
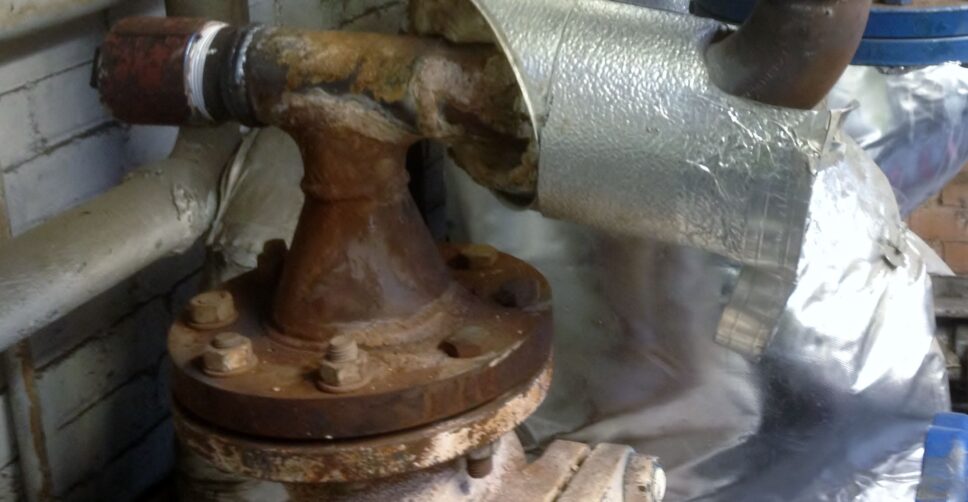
Process steam is the most efficient vehicle for heat transfer available to industry but for many reasons, we are seeing a decline in use in the public and to a lesser extent the private sector. Part of the reasoning behind the decline of use in the private sector in particular, is the fact that due to poor management of steam distribution systems they had become inefficient. If faced with an inefficient steam distribution system and under pressure from over-enthusiastic salespersons some in the NHS in particular have turned their backs on steam as a utility. The most cost-effective answer should have been improving process steam systems not removing them altogether; but in many hospitals, we have seen steam boilers disappear completely to be replaced by gas-heating and gas-heated water systems.
Was this ever the right answer or was this a knee-jerk reaction to problems that never really existed? Were perfectly good steam systems removed on the vague promise of short-term savings on energy consumption? In fact, why wasn’t improving process steam systems ever explored? We believe the simple answer in most cases is a complete lack of knowledge and understanding of the art of steam distribution, and we are certain our technical sales team can help.
Improving Process Steam Systems or the Art of Steam Distribution
Steam distribution systems are generally uncomplicated and if maintained an excellent source of process heat; steam temperature is easily controlled by raising and lowering the steam pressure and lower pressure can and does result in more efficient heat transfer. As you raise the pressure of the process, steam the temperature rises and at the same time efficiency in heat transfer falls; so to transfer heat efficiently, feed the heat exchanger at the lowest pressure possible.
To distribute your steam efficiently a higher pressure is required, this reduces the bore size of the distribution main and reduces heat losses as the steam condenses at a slower rate. So ideally, if you have a 10 bar rated steam boiler on your process steam system you can and should distribute process steam at that pressure then when it reaches the process or heat exchanger, reduce the pressure for efficient heat transfer. Consideration is then required at the ideal steam pressure for your process, the example below considers two different pressures to complete the same process.
- Steam at 7 bar for 1000 litres of water from 15°C to 75°C in one hour
- Steam load required 123kg/hr
- Steam at 3 bar for 1000 litres of water from 15°C to 75°C in one hour
- Steam load required 118kg/hr
The key to this difference is the fact that heat transfer is more efficient at lower pressures; now the difference does not look very much but imagine that is a heat exchanger running 10 hours a day in a 5-day working week and a 50 working week year to heat water for a process or a simple wash-down area.
- 5kg/hr x 10 x 5 x 50 =12,500kg/yr
Based on the average cost of process steam at around £18 per 1000kg is a saving of £225.00 per year. These figures, when you just say 5kg/hr, do not sound like a great deal but; if you also add in the cost to your carbon footprint these small savings can make a big difference to your business and the environment.
Some of the worst process steam systems in both the private and public sectors are those that have expanded existing steam mains, and have done so without looking at the most basic requirement, does my boiler produce the required amount of extra steam? Typical examples of this type of installation are additions to steam lines specifically sized for a single piece of equipment, now most installers will always leave some extra capacity in steam mains just for events such as this; but often what we add exceeds that capacity reducing efficiency to both steam users.
Time passes and the fact the steam main is not adequate is long forgotten and in some cases, further steam users are added to the same line. These circumstances are a regular event and if you add a lack of knowledge to the same scenario, additional pipework is often installed without dirt pockets, relay points or line ends resulting in the additional problem of poor-quality wet steam, water hammer and erosion.
Improving Process Steam Systems what are your options?
Improving process steam systems is not in many cases something complicated or has to cost a huge amount of money. In our experience, many process steam users explore the possibilities of improving process steam systems with what are sometimes large distributors and manufacturers of the relevant equipment. What they are often confronted with at the end of the process is quotes for huge amounts of equipment they do not necessarily need. Manufacturers and good distributors have a monopoly on the knowledge and understanding required and sometimes very much needed by the end user. Some but not all have been known to take advantage of this and the list of what is required to complete the works involved far exceeds what was expected.
The more complicated you make a steam system the more you can expect to go wrong, what if you installed an integrated steam trap monitoring system for instance that in a decade or so is obsolete? If this is what is required by your business then all is well but if what you want is simple process efficiency you do not need to know the immediate minute a steam trap failed its money for old rope. Steam trap monitoring can be achieved by buying the right ultrasound steam trap leak detector. My point is that many businesses will attempt to blind you with science and sell you a package tailored to massage their figures; here at Besseges (Valves, Tubes & Fittings) Ltd we will use our understanding of process steam issues to sell you the simplest most economical solution. Sometimes though the answer isn’t simple and on those occasions, we will still put forward the best possible answer and explain in plain English why, please contact us; we look forward to hearing from you.
Register For An Account
Save & manage your details, access invoices, and enjoy a quicker shopping experience!