Energy Efficient Steam Systems
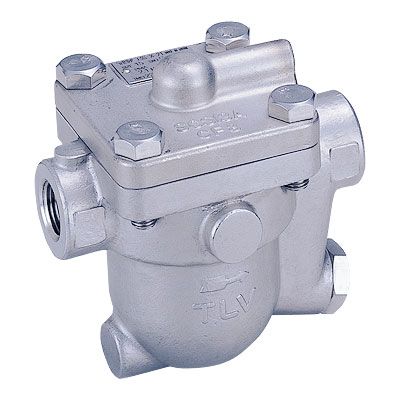
Process steam as a heat exchanger is highly efficient and offers excellent temperature control for many processes; here at ValvesTubesFittings.com, we can offer solutions that increase the possibility of energy-efficient steam systems. The keys to energy efficiency are many and varied; some of them are product-based and others are just simple best practices. This latest blog will explore some of the methods that can produce energy-efficient steam systems for your business now and in the future. For more information click read more or contact our excellent technical sales team.
Increase Steam Efficiency With Non-Discharged Condense Removal
Removing condense from your steam system is key to maintaining energy-efficient steam systems, as the steam contained within the system loses heat, condense forms and travels under the steam flow; this is known as non-discharged condense and can only be removed by placing line drain dirt pockets at around 30m to 50m intervals throughout your steam lines. Dirt pockets on the majority of steam systems are generally line-sized and should be fitted with the most efficient line-drain steam traps; historically line drain steam traps were in the main of the thermodynamic type. At present, modern line-drain free float steam traps in our opinion should be the steam trap of choice where practical. For the removal of non-discharged condense, there are three types of line drain dirt pockets, they are the basic inline dirt pocket, the relay point dirt pocket and the line end dirt pocket. Basic inline and relay point dirt pockets have a steam trap installed and line end dirt pockets have a steam trap and an additional air eliminator, please look at the illustrations provided to see a typical steam trap layout for each type.
Efficient Steam Systems – Entrained Condense Removal
Entrained condense are the water droplets contained in the steam flow travelling through your steam main, this cannot be removed via the line drains. To remove entrained condense a separator must be installed and many products are bulky heavy baffle-type separators requiring a great deal of support and the correct steam trap fitting to the outlet. Our solution for removing entrained condense from process steam is the TLV cyclone separator, these units are either standalone devices or incorporated in a pressure-reducing and control valve but all options come complete with a built-in free float steam trap. To achieve energy efficient steam systems this type of device is necessary and if installed at the point of use can increase heat transfer efficiency by up to 9%. If you would like to know more about, cyclone separators for steam or compressed air please contact us to discuss your requirements.
Managing Your Steam Trap Population
One of the most obvious methods of maintaining energy-efficient steam systems is good management of your steam traps, these devices if well maintained and tested for leaks at least annually keep processes more efficient. Despite this fact, many businesses still neglect their steam trap maintenance and very often are not aware of a leaking steam trap for many months. A visual inspection of a steam trap will offer no clue of a leak unless, of course, your business is one of the very few that openly drains condense to waste. There are sometimes signs in your hot well that a leaking trap does exist on a site, but these can only be identified under normal circumstances by using an ultrasound steam trap leak detector. If your business has not had a steam trap survey for over twelve months please contact us to arrange a quotation for your site or small steam trap populations we can offer a TLV Pocket Trapman. The TLV Pocket Trapman is an ultrasound leak detector complete with a thermocouple, which offers temperature as well as steam trap condition, with very little training, which is available upon purchase of the instrument; engineers or fitters can monitor steam trap performance as and when required. In addition, the TLV Pocket Trapman device is used to monitor pump bearings, over time this will produce a wear graph identifying worn and noisy bearings. For more information on process steam systems please follow our blog page here at ValvesTubesFittings.com or on our main website by following either link. Our highly respected technical sales team are available through our contacts page and can offer information on a wide range of pipeline pressure systems; we look forward to hearing from you and working with you to achieve energy-efficient steam systems.
Disclaimer: Information correct at the time of publishing (October 2016) but is subject to change. E&OE.
Register For An Account
Save & manage your details, access invoices, and enjoy a quicker shopping experience!