Corrugator Steam Systems Efficiency is Key
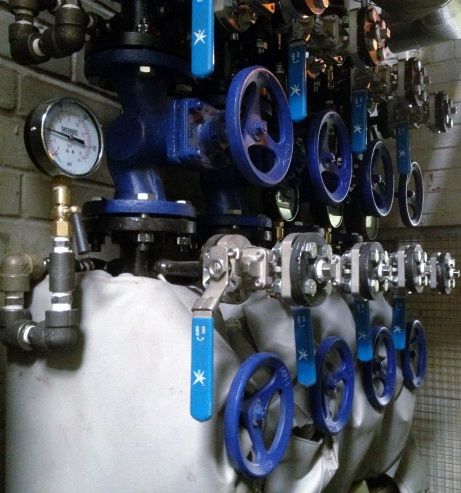
We have worked on a few sites with corrugator steam systems over the past 28 years and over this period we have learned a great deal. Our first customer back in 1989 was Dolan Corrugated Containers Ltd and this was our first involvement in supplying pipework, valves and fittings on a major steam installation. In the early 1990s, this business installed their new corrugator and so began our association with corrugator steam systems.
The following blog will explore our interest and increased knowledge of the workings of corrugator steam systems, and I hope that those who take the time to read it will consider our business as a potential supplier of steam system products now and in the future. For those having a cursory glance at this post, contact our technical sales team for more information.
Corrugator Steam Systems Steam Traps
Probably our greatest involvement in corrugator steam systems has been in the specification of the correct steam traps for a given process. We have noted over the past few decades that many manufacturers have offered different approaches for steam traps on these systems.
In some cases, the specification of incorrect steam traps has been costly and time-consuming. Probably the best example of this was the advice from a competitor through an inexperienced sales engineer; replacing 26 steam traps from float type to bucket type. The result of this was the loss of production and the costly replacement of the original steam traps; but more to the point the complete loss of faith in a leading manufacturer.
A huge part of corrugator steam systems is the many rollers used to transfer heat to complete corrugated sheets. Which is manufactured at various temperatures depending on the thickness and quality of the paper required. In our experience, the variations in pressure could be anything from 2 to 12 bar to achieve different temperatures. Saturated steam used to produce efficient heat transfer increases in temperature as the pressure rises.
The temperature of saturated steam is a fixed value depending on the pressure; for example, saturated steam at 10 barg is 184.1°C and at 5 barg it is 158.9°C. Therefore, process steam correctly controlled is highly efficient at process temperature control across many manufacturing operations; from the manufacture of cardboard boxes to the cooking of large batches in the food industry.
We digressed somewhat from the core subject here corrugator steam systems and the next paragraphs will explain why we believe certain steam trap types should be installed on corrugator steam systems. The understanding that leads us to the following conclusions is based on actual experience with two manufacturing sites.
Corrugator Steam Systems Steam Trap Selection
Returning to the heart of the process of heat transfer on corrugator steam systems; you have cylinders heated by saturated steam at varying pressures as previously mentioned. Selecting the correct steam trap for a wide range of temperatures can be difficult as the volumes and differential pressures can vary significantly.
So, what is required is a steam trap that will be operated efficiently across the differences and possibly the worst option would be a trap with a fixed orifice. Consider your process requirement can alter between the pressures we have already discussed. The product requires a lower temperature, for example on the use of printed paper.
The temperature selected is 158°C so the steam pressure is 5 bar, consider then the pressure drop across the process as steam condenses; and then any back pressure exerted by the design of the condense return. The differential pressure could be 3 to 3.5 bar as an example, trap selection is then simple; your steam trap would have a 4.5 or 5 bar orifice.
But then the following requirement is a heavy-duty plain box requiring a much higher temperature, for example, 185°C and the steam pressure required is doubled to 10 bar. The requirement of the orifice size has changed to a new differential pressure and you have a fixed orifice installed which would then drastically decrease condense removal; thus, affecting process temperature and the finished product.
Resolving this issue is simple, steam trap selection should allow for both possibilities and any others in between. A fixed orifice steam trap is not in our opinion the right solution. In this case we would offer a free-float mechanical steam trap with a 13-bar orifice; covering all the possibilities within the differing pressures we have previously mentioned. All that is missing from this steam trap selection is concluded in the next paragraphs, covering steam lock release.
Corrugator Steam Systems Steam Locking
Corrugator steam systems are prone to the phenomenon of steam locking, which is due to the design of the method of condense removal. Simply put condense is removed from the cylinder through a dip pipe connected to the rotary union. The rotation of the cylinder displaces the hot condense within it, if the condense was at a fixed point this would not occur.
The faster the cylinder rotates the more turbulent the condense becomes within the cylinder; resulting in the dip pipe passing in and out of the condense. This then allows steam to pass through, locking out the steam trap on each occasion. Once the steam condenses the steam trap then continues normal operation.
On each occasion, steam enters the trap though it will do what it is designed to do, trap steam. This continuous part of the process then reduces the overall temperature of the roller and this temperature reduction can be measured at the steam trap. In our experience, this can result in a reduction in temperature at the steam trap of anything from 10°C to 20°C. If the steam trap temperature is reduced, then the process temperature is reduced and ultimately less efficient.
Corrugator Steam Systems Steam Locking Prevention
Preventing steam locking in corrugator steam systems or in fact most processes that operate with drying cylinders is a must. Steam locking can and does vary greatly the process temperature and within our own experience; we have increased the temperature at the steam trap by as much as 20°C. This has been achieved by fitting lock release valves to the existing steam traps or replacing them with traps that have this ability.
A steam lock release valve on a TLV free float steam trap is under most circumstances a needle valve that acts on the X-Element or bimetal air release. This needle valve can be set to an optimum point which, causes the small amount of steam locking out the trap to leak via the air venting path. The small leak then prevents the steam trap from locking, increasing the temperature at the trap and within the process.
Steam locking can cause an increase in the use of process steam, temperature drops within the process; can prompt control valves to increase steam flow to counter the effect. This could result in increases in the cost of processing steam and of course less efficient production.
For more information on purchasing steam traps for your corrugator steam systems; or for that matter any other process steam application please contact our technical sales team. We also can offer a service to set the lock release valves following installation; subject to safe access and the site location. This service does come at a cost which can be agreed in advance and the team at Besseges (Valves, Tubes & Fittings) Lyd look forward to hearing from you.
Register For An Account
Save & manage your details, access invoices, and enjoy a quicker shopping experience!